The Scientific Research Behind Porosity: A Comprehensive Guide for Welders and Fabricators
Recognizing the intricate systems behind porosity in welding is important for welders and producers striving for impeccable workmanship. From the composition of the base products to the details of the welding process itself, a wide range of variables conspire to either aggravate or minimize the existence of porosity.
Understanding Porosity in Welding
FIRST SENTENCE:
Examination of porosity in welding discloses vital insights into the honesty and top quality of the weld joint. Porosity, identified by the existence of dental caries or spaces within the weld metal, is an usual issue in welding processes. These spaces, otherwise appropriately addressed, can compromise the architectural honesty and mechanical residential or commercial properties of the weld, leading to possible failings in the ended up item.
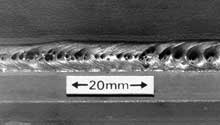
To identify and quantify porosity, non-destructive screening techniques such as ultrasonic screening or X-ray assessment are often utilized. These techniques permit for the identification of internal issues without jeopardizing the stability of the weld. By evaluating the dimension, shape, and circulation of porosity within a weld, welders can make enlightened choices to enhance their welding processes and accomplish sounder weld joints.
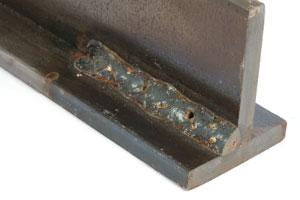
Variables Affecting Porosity Formation
The occurrence of porosity in welding is influenced by a myriad of aspects, ranging from gas securing efficiency to the intricacies of welding specification setups. One important variable adding to porosity development is insufficient gas protecting. When the shielding gas, usually argon or CO2, is not successfully covering the weld swimming pool, atmospheric gases like oxygen and nitrogen can pollute the molten metal, leading to porosity. Additionally, the sanitation of the base materials plays a considerable duty. Contaminants such as corrosion, oil, or wetness can evaporate throughout welding, creating gas pockets within the weld. Welding criteria, consisting of voltage, present, travel rate, and electrode type, additionally effect porosity development. Using inappropriate settings can generate too much spatter or warm input, which subsequently can cause porosity. Furthermore, the welding strategy used, such as gas steel arc welding (GMAW) or protected steel arc welding (SMAW), can affect porosity formation as a result of variants in heat circulation and gas insurance coverage. Recognizing and regulating these variables are necessary for lessening porosity in welding procedures.
Effects of Porosity on Weld High Quality
Porosity formation substantially jeopardizes the structural stability and mechanical buildings of welded joints. When porosity exists in a weld, it creates spaces or tooth cavities within the product, lowering the total toughness of the joint. These voids serve as anxiety focus factors, making the weld more prone to fracturing and failing under load. The presence of porosity likewise deteriorates the weld's resistance to deterioration, as the trapped air or gases within the spaces can react with the surrounding setting, leading to degradation in time. Furthermore, porosity can impede the weld's capacity to endure stress or effect, further jeopardizing the overall high quality and dependability of the welded framework. In critical applications such as aerospace, automotive, or architectural buildings, where safety and resilience are extremely important, the detrimental effects of porosity on weld quality can have severe effects, stressing the relevance of decreasing porosity via appropriate welding Going Here methods and procedures.
Techniques to Decrease Porosity
To my company improve the quality of bonded joints and ensure architectural integrity, welders and makers utilize specific methods targeted at reducing the formation of gaps and tooth cavities within the product during the welding procedure. One reliable technique to decrease porosity is to ensure appropriate material prep work. This consists of comprehensive cleaning of the base steel to get rid of any contaminants such as oil, grease, or wetness that can add to porosity formation. Furthermore, making use of the suitable welding specifications, such as the appropriate voltage, present, and take a trip rate, is critical in avoiding porosity. Keeping a consistent arc length and angle during welding also helps in reducing the chance of porosity.

Utilizing the straight from the source proper welding technique, such as back-stepping or utilizing a weaving motion, can likewise help disperse warm evenly and reduce the opportunities of porosity formation. By applying these methods, welders can efficiently minimize porosity and generate premium welded joints.

Advanced Solutions for Porosity Control
Carrying out cutting-edge innovations and cutting-edge methods plays a critical duty in accomplishing remarkable control over porosity in welding procedures. Additionally, utilizing innovative welding techniques such as pulsed MIG welding or customized ambience welding can additionally assist minimize porosity issues.
One more innovative solution includes using advanced welding tools. For example, using equipment with built-in functions like waveform control and sophisticated source of power can boost weld top quality and decrease porosity dangers. The application of automated welding systems with exact control over criteria can dramatically decrease porosity problems.
Moreover, integrating sophisticated monitoring and examination modern technologies such as real-time X-ray imaging or automated ultrasonic testing can aid in identifying porosity early in the welding procedure, permitting prompt rehabilitative activities. In general, incorporating these sophisticated options can considerably boost porosity control and improve the overall top quality of bonded components.
Verdict
In conclusion, recognizing the science behind porosity in welding is necessary for welders and producers to generate high-grade welds - What is Porosity. Advanced services for porosity control can better improve the welding procedure and ensure a strong and trusted weld.
Comments on “What is Porosity in Welding: Understanding Its Reasons and Enhancing Your Abilities”